Vorbereitung der Rohhaut
Den ersten Schritt der Lederherstellung bildet die Vorbereitung für die Gerbung. Dazu gehören die gekühlte Lagerung und das Sortieren der Qualitäten. Außerdem wird die Haut in der Weiche von Schmutz und Konservierungssalz befreit.
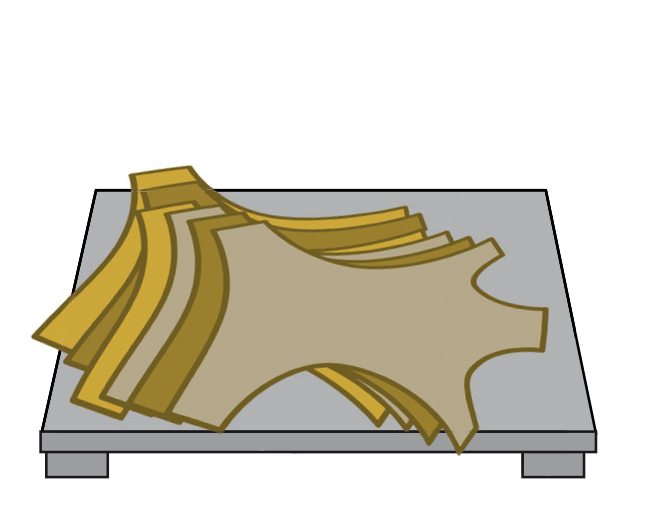
Lagern und sortieren
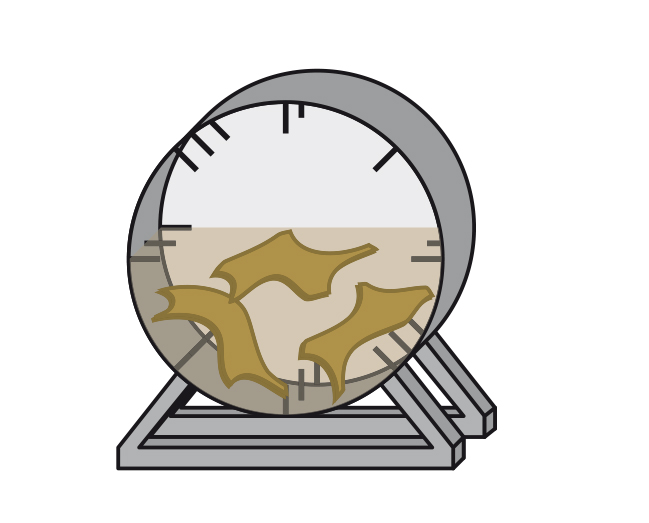
Weichen
Von der Rohhaut zur Blöße
Anschließend werden die Teile der Haut, die nicht in Leder umgewandelt werden können, entfernt. Die Häute werden im Äscher enthaart. Beim Spalten trennen die Ledermacher den „Narbenspalt“ für Glattlederarten und den „Fleischspalt“ für raue Spaltleder voneinander. Am Ende steht die optimal vorbereitete Tierhaut – die sogenannte Blöße.
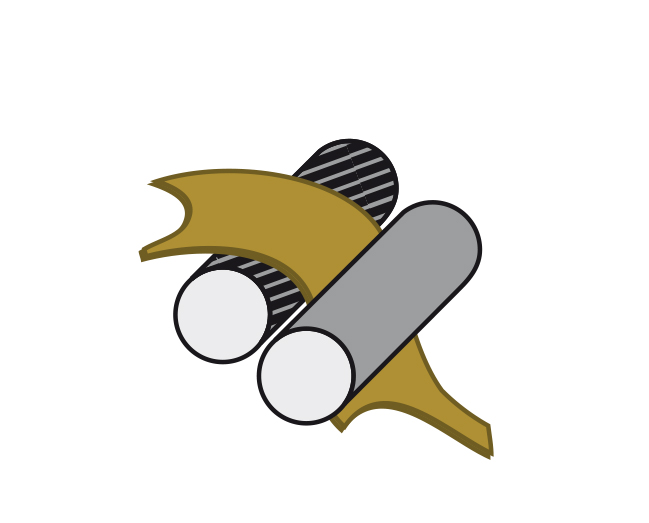
Entfleischen
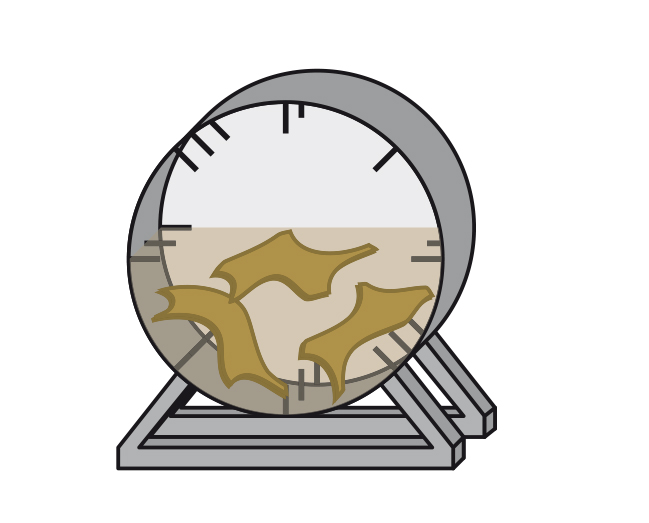
Äschern
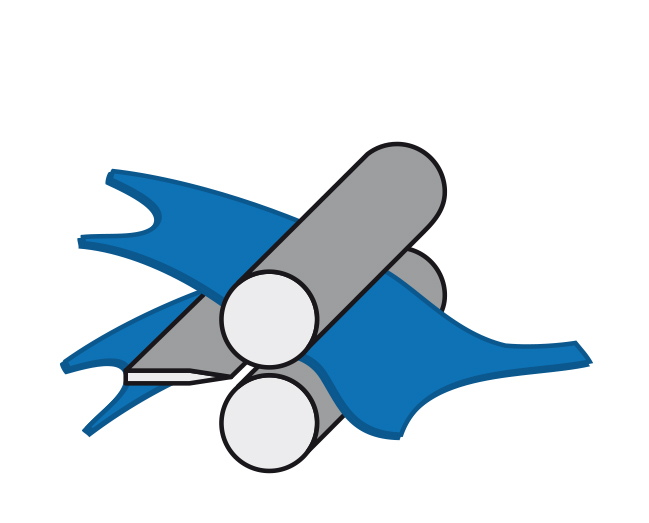
Spalten
Hauptgerbung
Auf die Blöße lassen erfahrene Fachleute ausgewählte Gerbstoffe einwirken – abhängig von der gewünschten Lederqualität. Durch die Gerbung entsteht Leder. Anders als die ursprüngliche Haut ist es widerstandsfähig, fäulnisbeständig, lager- und transportfähig. Welche Gerbmethode bei der anschließenden Nachgerbung zum Einsatz kommt, hängt vom Verwendungszweck ab. Während für Schuhsohlen ausschließlich eine Gerbung mit Pflanzenextrakten von Kastanie, Eiche oder Mimosa in Frage kommt, wird für Polster-, Ober- und Feinleder die mineralische Chromgerbung verwendet. Die sogenannte chromfreie Gerbung, die unter anderem Vorteile beim temperaturbedingten Schrumpfen des Leders aufweist, ist in der Automobilindustrie gefragt.
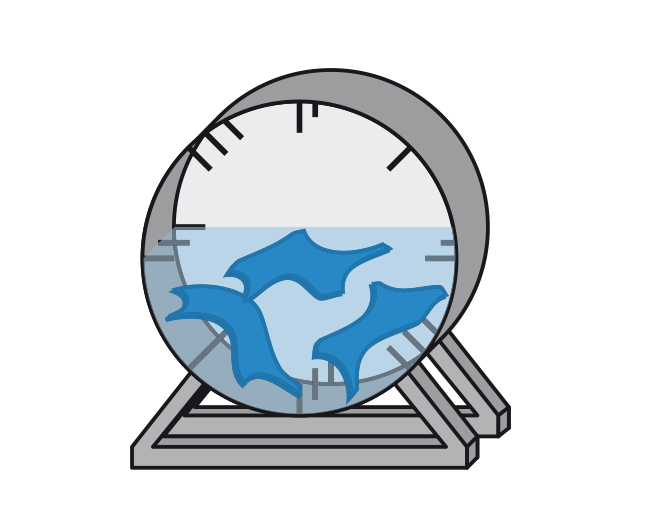
Gerbung
Weitere Arbeitsschritte
Die Leder werden entwässert, nach Qualitätskriterien sortiert, und das Narbenleder wird durch das Falzen auf die gewünschte Stärke gebracht.
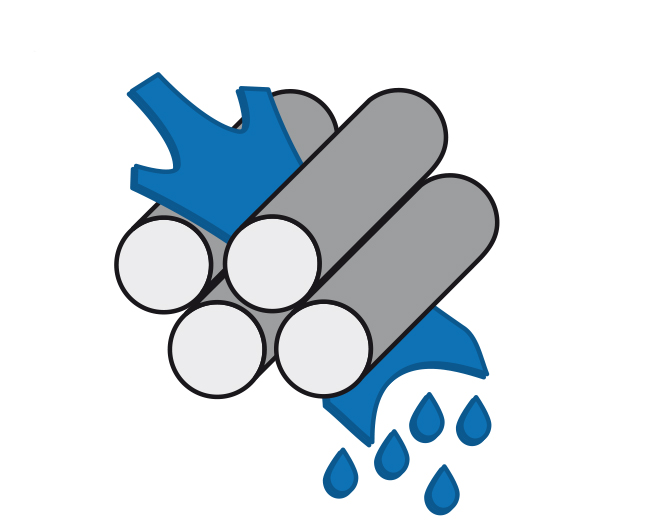
Abwelcken
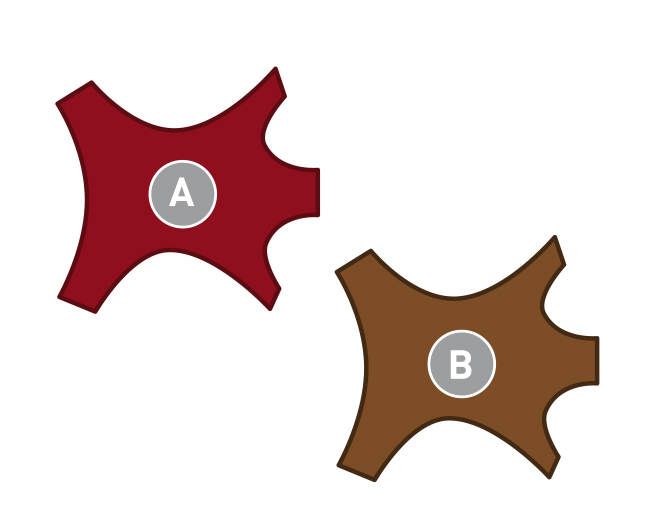
Sortieren
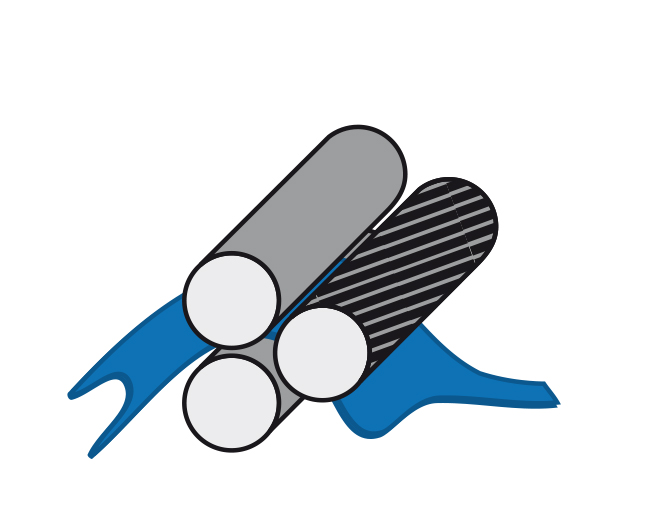
Falzen
Neutralisieren, Füllen, Färben, Fetten
Seinen endgültigen Charakter erhält das Leder in der sogenannten Nachgerbung. Dabei kommen pflanzliche, synthetische oder mineralische Nachgerbstoffe zum Einsatz. Darauf folgen die Färbung, eine Fettung für die Geschmeidigkeit sowie eine mechanische Auflockerung der Faserstruktur, um Eigenschaften wie Elastizität oder Weichheit zu fixieren. Eine Imprägnierung, um die Wasseraufnahmefähigkeit zu reduzieren, bildet abhängig von der Verwendung den Abschluss dieser Arbeitsschritte.
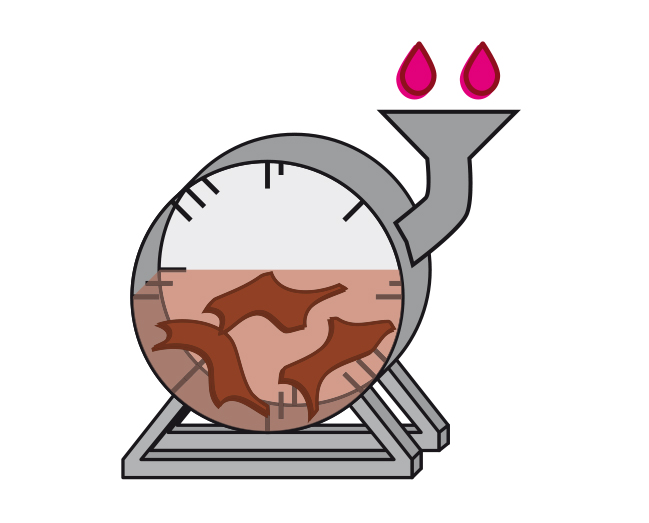
Neutralisieren, Füllen, Färben und Fetten
Ausrecken und Zurichtung
Die Leder werden getrocknet und zum Weichmachen gewalkt. Im letzten Fertigungsschritt, der sogenannten Trockenzurichtung, erhält das Leder sein endgültiges Gesicht und den letzten Schliff. Dazu dienen eine Reihe von mechanischen und chemischen Behandlungen. Insbesondere die optischen und modischen Merkmale des Leders werden dabei optimiert. In diesem Prozess erhalten die unterschiedlichen Ledersorten zudem ihre typische Ausprägung, wie beispielsweise die samtig weich angeschliffenen Nubukleder. Durch Bedrucken oder Prägen entstehen Muster oder attraktive Oberflächen.
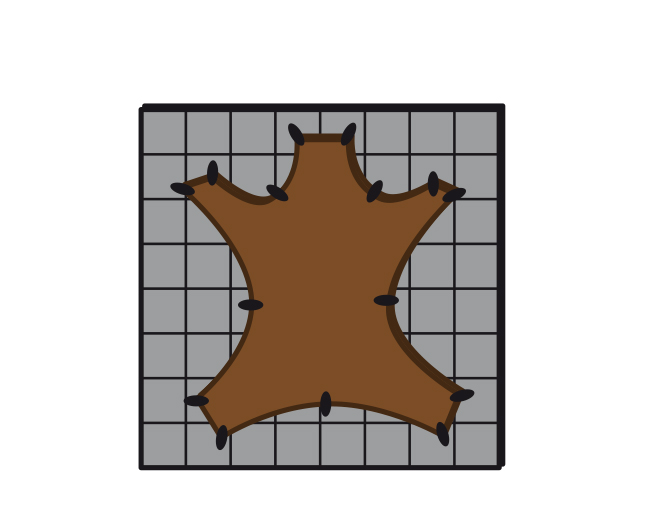
Ausrecken, Trocknen
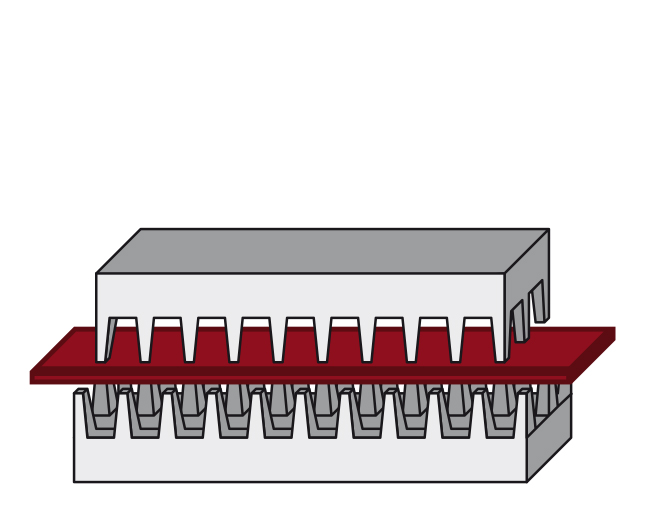
Stollen
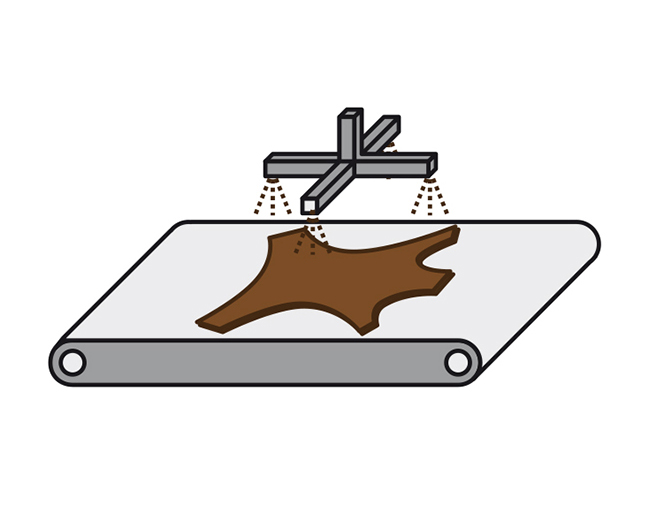
Zurichten
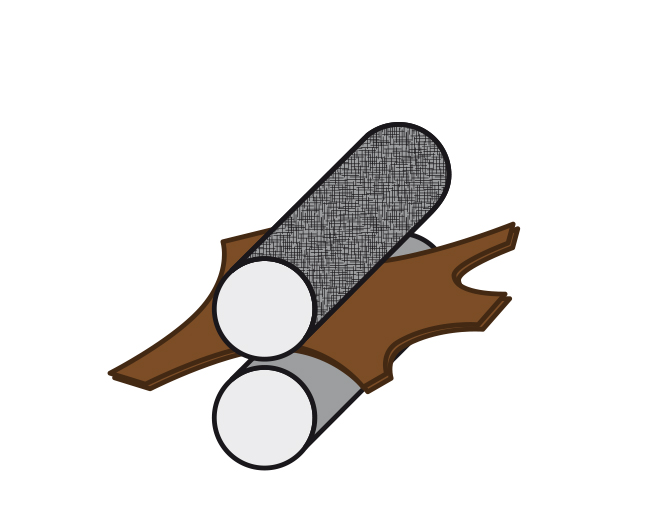
Zurichten